

We use safe a 35 KHz ultrasonic frequency and to avoid standing waves that reduce efficiency, we add a 70 KHz passive resonance. Contaminants and residues from prior cleanings are removed first, then the release agent that has captured dirt, dust, etc. The above image shows the same grooves BEFORE and AFTER the Kirmuss Restoration Process. Further, our patented process assures the records are suspended at the proper height irrespective of the record size without damaging the label. Removed, the needle no longer hits these contaminants and finally makes proper contact with groove details. It is here where the nasty pops and clicks reside: micro-welded dust in the release agent of a new or vintage record. We designed our process to first clean the surface of the record, then the grooves, RESTORING the record, including the removal of the release agent residue. It just agitates the soap used in the water basin.
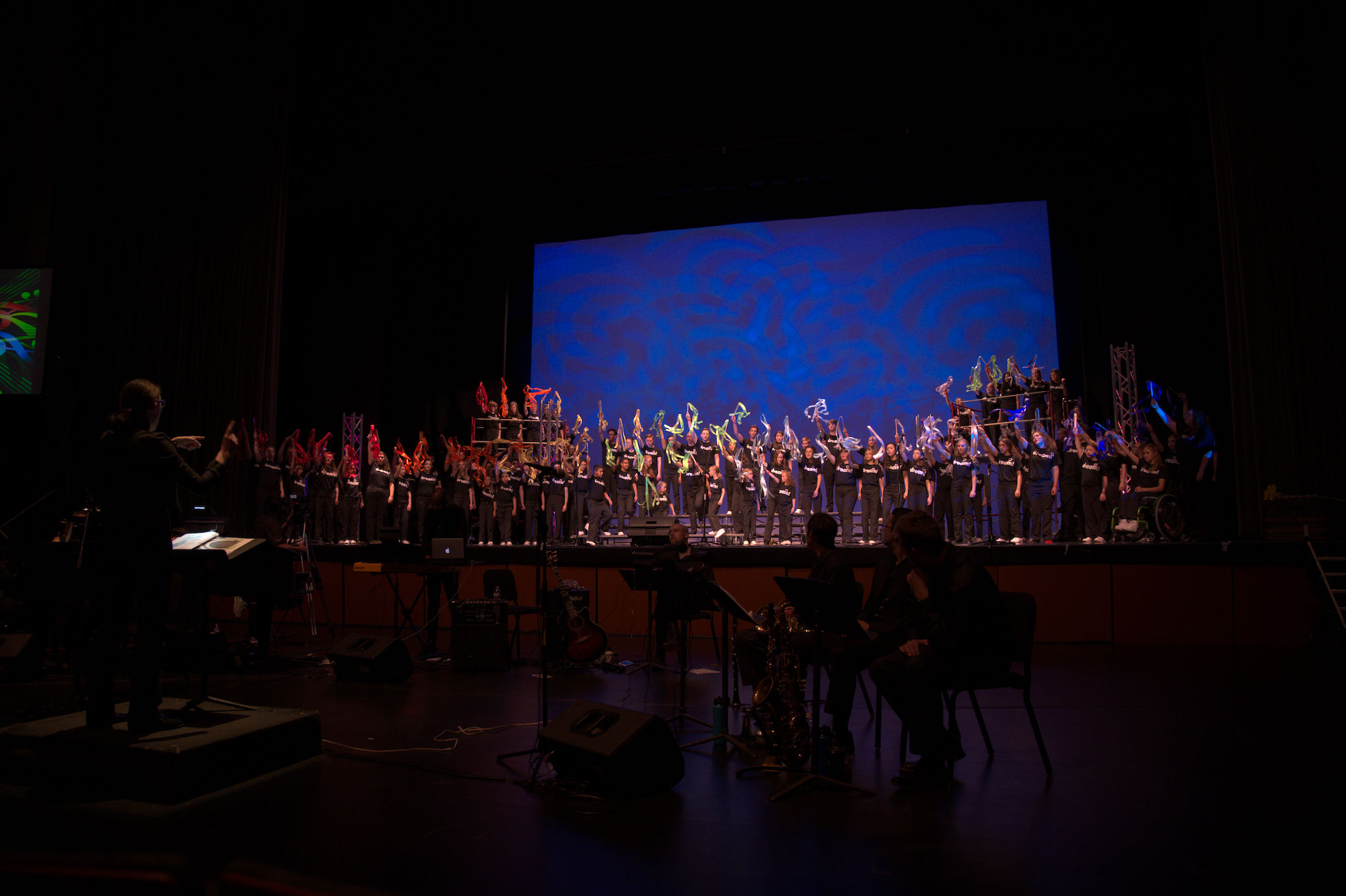
In fact, this 40 KHz sonic is actually a sonic bubbler, and does not use cavitation. Fungus removed but not the dust held in the groove by the record's release agent.
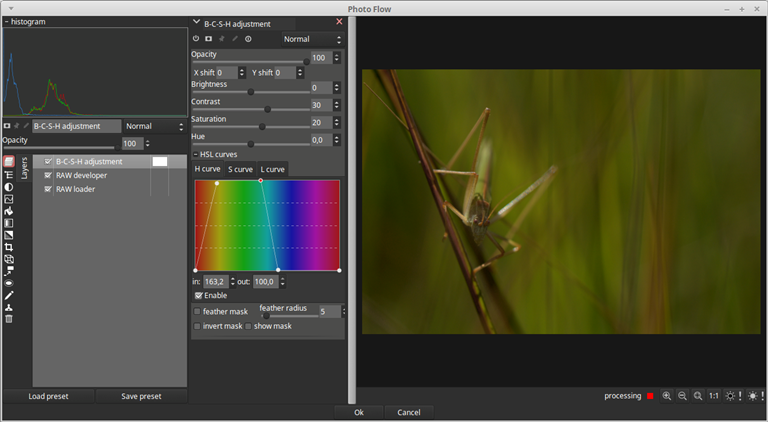
We restore the grooves! Below is an image of fungus on a record’s surface and groove left over after cleaning by an advertised 40 KHz ultrasonic at 4 times the price of the KA-RC-1. This is as most processes just surface cleans at best. >AS TO RESULTS: Exclusively no one speaks about “db signal gain” after a cleaning. Second: Seems where no one understands that PVC repels water, so with or without the presence of cavitation, one needs to change the charge of the record as we do over several cycles as to remove first films left by other cleaning processes either air dried or vacuum dried, then the release agent from the time of pressing.
Photoflow relight professional#
First: NO ONE SEEMS TO USE THE ALUMINIMUM FOIL TEST OR TEST EQUIPMENT EXPECTED TO BE USED BY A PROFESSIONAL SONIC MANUFACTURERS TO CHECK TRANSDUCER OPERATION. No one uses microscopic analysis or signal analyzers to evaluate their process. As such: Many processes have been designed without understanding how records are made, their composition, and how various cleaners or processes may affect the records themselves. Using the universally recognized aluminum foil test on these machines made in Germany and in the Baltic States and Hong Kong ARE SONIC BUBBLERS. SOME 40 AND 120 KHZ MACHINES ADVERTISED AS ULTRASONICS AFTER TESTING WITH ALUMINUM FOIL DO NOT USE ULTRASONIC CLEANING ACTION BY WAY OF CAVITATION. In fact, we found that most if not all processes only focus on cleaning the record’s surface.
Photoflow relight plus#
By changing the colour of light, photopolymers can be recycled and reshaped, allowing these macromolecular precursors to be applied to reversible and photodegradable material design.We have spent 7 plus years in researching all past and current processes and methods to clean records.
Photoflow relight Offline#
Size exclusion chromatography provides additional offline analysis of both the polymerisation and photodegradation over time. The process was monitored online via a photoflow – high resolution electrospray ionisation mass spectrometry setup (ESI-MS).
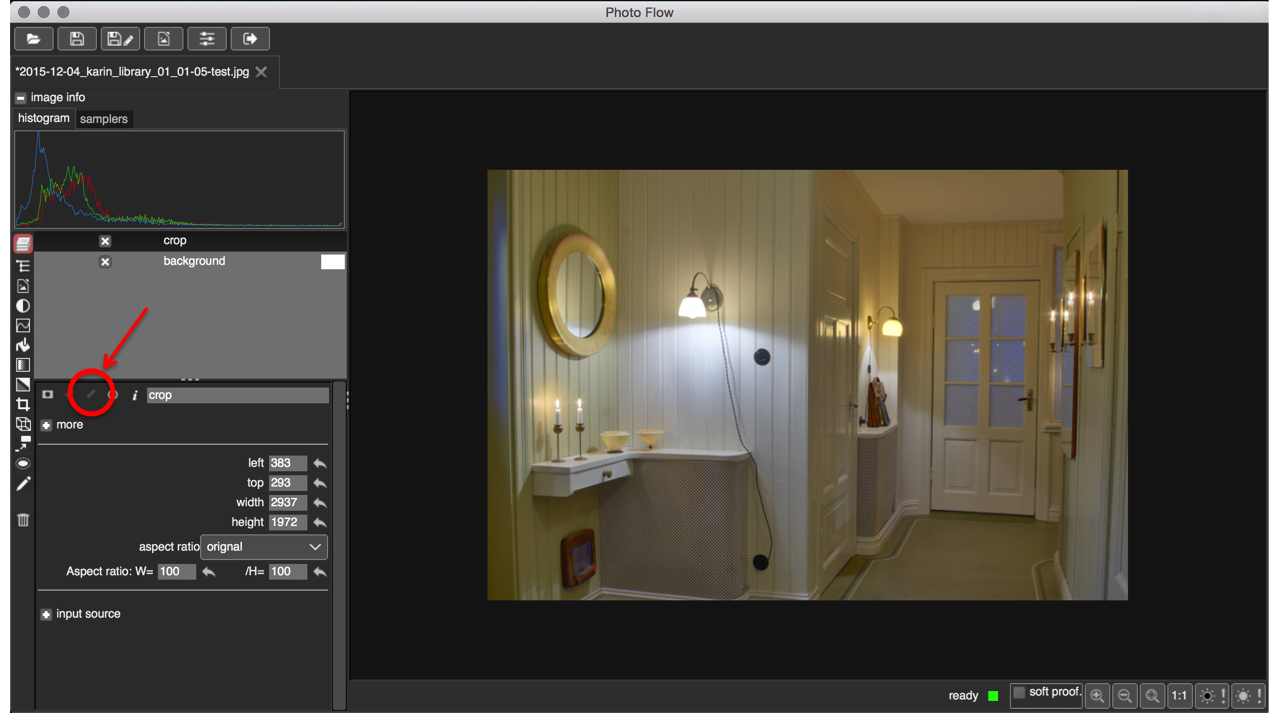
Violet blue light at 415 nm triggers -cycloadditions of a pyrene-chalcone derivative to grow linear step-growth polymers, while subsequent UV-B light irradiation triggers the depolymerisation. Both a batch approach and a continuous photoflow setup are employed to investigate the degree of polymerisation and scalability. Herein, we demonstrate the scalable synthesis of catalyst-free, visible-light mediated photo-oligomers and -polymers via a step-growth mechanism. Light as a non-invasive and clean external stimulus provides a facile route towards macromolecular design.
